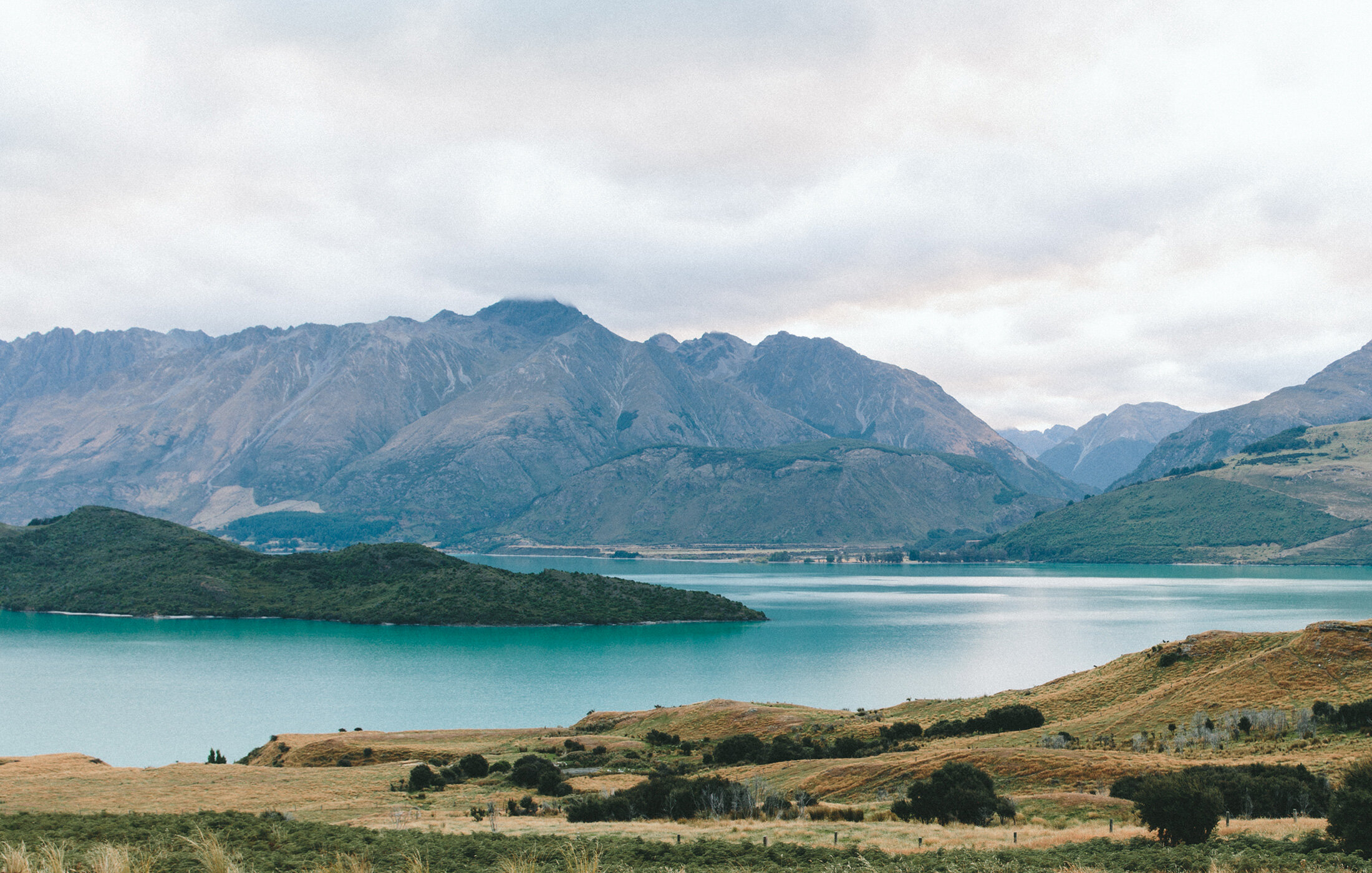
Project 2: Soldering Fume Extractor
As I mentioned in Project 1, I was soldering more and more at home. Little bits and pieces here and there for work. Nothing crazy, just some small SMDs for prototypes. I didn’t have a proper soldering station set up at home though, and as you might imagine, the safety tools are rather critical. At work, we had a few Hakko fume extractors that seemed to work pretty well. I wanted to buy one, but for $75, I thought this might be a relatively simple DIY project instead.
Project Goals
Make a more functional fume extractor
Learn basic electronics
Develop and design with more advanced modeling techniques in Fusion 360
It didn’t take long for me to understand how the fume extractor works. At its core, its a fan intake and an activated carbon filter. Add a plug and an on/off switch, and badabing - badaboom. I’ve used the Hakko one for several months, and while its effective, there was room for improvement over the manufacturer’s design. One thing I liked was that it was relatively quiet and strong, most likely a result from a high quality fan motor. It pulled in plenty of air. However, it was bulky, and not adjustable, meaning you had to have it within six feet of a power source and withing about a foot of your work space. The fan, being not able to tilt meant that if I needed to re-orient my workspace to get a better angle on a solder joint, I would need to move the whole fan as well. I know it doesn’t sound that bad, but its a nuciense when you have lead solder in one hand, a 600*C iron in the other, and a gaggle of sensitive electronic prototypes in front of you, with a dozen more solder joints to go. Well, maybe I’m just being dramatic. what everrrrrrr…
So what do I want in a fume extractor? I started with wanting something small, and attached to an adjustable tube to easily direct airflow. Ideally also battery powered so its portable and stowable when not in use; I don’t need or want this on my desk when I’m not soldering. And that was it, those were my requirements.
V3 - I was nearing the end of the amount of effort I wanted to put into this project. But there were a few things I needed to fix before I call it complete (at this point, complete = good enough). Starting with the frame, the previous design had the frame in two seperate parts. The reason for that was mostly for an easier time prototyping. I knew that having the frame in one piece was critical to minimize any airflow leakage, so I just attached the two bodies and adjusted some of the edges to fix that. Next thing to tackle was making a mount for the stand such that the fan had a way to exhaust air. I opted for a simple angled mounting bracket that the could simply attach to the bottom.
Make it stand out
V2 - In my mind, there were two areas that obviously needed improvement: 1) airflow and 2) electronics. I tackled both of these in parallel, which I later realized was important, as the things I was learning in one subject directly translated to a shift in strategy in the other area. I’ll explain more below.
I never took a fluids class in college, but if I did, I’d imagine this concept is taught on day 1: if I wanted to increase airflow velocity, I would need to either increase the fan speed, or decrease the cross-sectional area of the duct. I found a bend-and-stay duct that would be perfect for this application on McMaster, along with the accompanying rubber fittings. This was a nice solution because it allowed me to move the intake to the right position without needing to move the whole fan rig.
I chose to ramp up the fan by choosing a more powerful 12v Noctua fan, specifically the NF-F12 iPPC 3000. Being a four pin fan, you can actually controller the fan speed, but after reading the spec sheet, I discovered that leaving this pin disconnected would just make the fan spin at full speed, which is perfectly fine for this application. And considering this is now a 120x120mm fan, I needed to redesign the housing for all of this. There were several new modeling tools I used for this rev. One was the pattern tool, allowing me to replicate a hexoganal shape on the outflow vent in the back. This was really just to hold everything in place. I also got to play around with the loft tool. I used this in the previous prototype, but this model used this much more extensively allowing me to experiment with different loft types and features. It became immediately apparent that these are crucial to a modelers arsenal.
At this point, aside from connecting more batteries to this 12v fan, I needed to identify a better solution. There were a handful of DIY fume extractor guides out there, and I was able to learn a lot from them. Additionally, I learned a lot from a coworker about LiPo battery charging and using batteries for powering electronics. These lead me to realize that I needed a battery management device, and a low voltage boost converter. The concepts of each of them seemed fairly straightforward; the BMS would safely handle battery charging, while the boost converter converted the 3.7v output of the LiPo to the correct 12v needed for the fan. After a couple of youtube videos, I settled on a Sparkfun Battery Babysitter and an Anmbest Mini Boost Module. Both of these need a small bit of configuration to get started, such as setting the output on the boost converter to 12v by soldering some on-board pads, but nothing too crazy.
There were a few things I skipped out on during modeling this prototype, but I’m going to justify that by saying it was easier to print, and I was more of a functional test more than anything else. But upon putting it all together, I’d say conceptually, it worked alright. The shortcuts were very apparent though. I didn’t realize it when I started this design, but it became apparent quite quickly that this could not hold itself upright due to the weight of the bend-and-stay ducting. There was also a sizable gap between the filter and the fan that could be lessened. But perhaps most importantly, the suction power of the fan worked quite well! The duct needed to be about 6 inches away from the solder joint to be effective, which was far enough for it to be out of the way during use.
Make it stand out.
It all begins with an idea. Maybe you want to launch a business. Maybe you want to turn a hobby into something more. Or maybe you have a creative project to share with the world. Whatever it is, the way you tell your story online can make all the difference.